The invention of silicon chips revolutionised communications. Even today they are the cornerstone of the technologies we use to move information around the world.
The way they work has changed significantly, however. They have become better: for a long time this was because experts improved its hardware to operate as efficiently as possible. But more recently, researchers have started to replace the electrons with photons, the particles of light, as the agents responsible for storing and manipulating information.
Thus today we have silicon photonics with valuable applications in data centres and sensors as well as potential ones in quantum computing. Silicon photonics is quickly gaining traction due to the many advantages it offers over traditional semiconductor chips.
In a study in Nature, scientists from the US and Europe reported that they had successfully fabricated the first miniaturised lasers directly on silicon wafers, marking a significant advance in silicon photonics.
Photons carry information faster, with greater data capacity, and lower energy losses than electrons.
But photons aren’t silver bullets. A significant challenge associated with using photons is integrating the source of these particles — a light source — with the silicon chip itself.
Currently, engineers’ best bet is to attach a separate laser light source to the chip. The resulting device operates more slowly than a chip with an integrated light source because of the small but significant mismatches that arise due to being manufactured independently. Separately manufacturing and attaching the lasers is also more expensive.
In the new study, the researchers surmounted this problem by ‘growing’ the laser directly on a silicon chip, in a process that is also more scalable.
The research team also conducted its entire process in a standard complementary metal-oxide-semiconductor (CMOS) manufacturing line, which the technology industry currently uses to manufacture electronic chips. Thus the new technique could be compatible with existing manufacturing methods.
Getting on the chip
A typical silicon chip has four components: a source to produce the electrons or photons, waveguides, modulators, and photodetectors.
In a photonic chip, a laser is the light source. This is the hardest part to make on the silicon chip itself. The waveguides act as paths for the photons, similar to how wires are paths for electrons.
Modulators are devices that encode information onto light (or decode information from a light signal). They do this by transcribing the information in some physical property of the light, like varying its intensity, wavelength or phase. (Similarly, they extract information by ‘reading’ these variations in an incoming carrier signal.)
Finally, photodetectors convert light into electrical signals.
Switching the laser on
In its simplest form, a laser — an acronym of ‘light amplification by stimulated emission of radiation’ — works by amplifying light in a process called stimulated emission.
Here, an electron in a higher energy level is ‘kicked’ by an incoming photon to lose some energy and drop to a lower energy level. This energy lost is in the form of another photon whose energy matches that of the incident photon. When this process occurs repeatedly, the population of electrons generates a coherent beam of light. This is a laser.
Silicon itself can’t emit light efficiently as it has an indirect bandgap. In other words, in a silicon atom, an electron in a higher energy level cannot drop to a lower one on its own; instead it requires an additional particle to help release the electron’s energy and drop down.
Most lasers use semiconductor materials like gallium arsenide to produce the light. These materials have a direct band gap, meaning that electrons inside the material can drop from a higher energy level to a lower one by emitting a photon.
Direct band-gap materials allow electrons to directly emit photons without requiring to be kicked, converting more electrical energy into light without additional interactions. Thus the laser is more energy-efficient.
Integrating gallium arsenide with silicon is a major challenge because of the different arrangement of atoms in each of the elements. When gallium arsenide is grown layer by layer on silicon, the mismatch in the crystal structure of the materials causes imperfections where the atomic patterns don’t line up properly.
Imagine trying to fit two puzzle pieces together when they are not part of the same puzzle.
When electrons encounter these defects, they lose energy as heat rather than as light, rendering the laser less efficient.
In the trenches
In their study, the researchers successfully created a chip that consisted of a silicon wafer base, nanometre-sized ridges through which photons travelled, and a small region that produced these photons.
The idea of the ridges came from a 2007 study, in which researchers from AmberWave Systems Corp. found that if gallium arsenide is deposited on silicon at the bottom of a narrow, deep trench surrounded by an insulating material, the defects become ‘trapped’, meaning they don’t interfere with the laser’s ultimate operation.
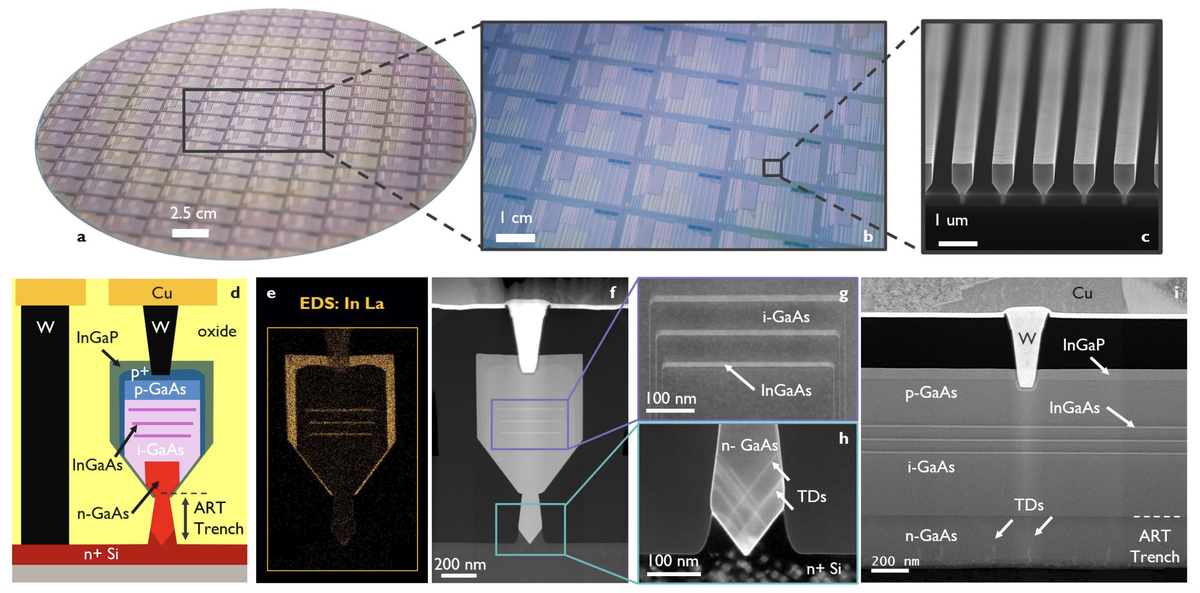
Top, L-R: photograph of a fabricated 300-mm silicon wafer containing thousands of GaAs devices; close-up view of a fabricated 300 mm wafer showing multiple dies; and scanning electron micrograph of a GaAs nano-ridge array before encapsulation. The bottom row shows various components of chip.
| Photo Credit:
arXiv:2309.04473v1
So the researchers carved nanometre-wide ridges in a 300-mm long silicon wafer, and applied silicon dioxide as the insulating material. Any defects were confined to the bottom of these trenches, allowing a defect-free gallium arsenide crystal to grow above.
Next, on the same wafer, the researchers deposited three few-atoms-thick layers of indium gallium arsenide (i.e. gallium arsenide where 20% of gallium atoms had been replaced with indium to achieve optimal light emission). These layers together functioned as the laser.
Finally the team deposited a layer of indium gallium phosphide on top of the whole setup for protection.
To make the laser work, the researchers added electrical contacts connected to an external current source. When a current flowed into the indium gallium arsenide region, the latter emitted photons that flowed through the waveguides.
Solving a long-standing problem
The researchers were able to embed 300 functional lasers on a single 300-mm silicon wafer.
The size of the wafer is important because it’s the industry standard in modern semiconductor manufacturing, and can thus be integrated without demanding significant changes.

The laser produced light with a wavelength of 1,020 nm, which is well-suited for the short-ranged transmissions between computer chips.
Thus the researchers expect their chip could lead to a substantial improvement in computing performance and reduce energy consumption in data centres.
The threshold current required to run the laser was as little as 5 mA, comparable to that required for an LED in a computer mouse. The laser’s output was around 1 mW.
The laser could continuously operate for 500 hours at room temperature (25° C). At around 55°C, its efficiency dropped.
While this duration is promising, recent research on optical silicon chips has demonstrated continuous operation at temperatures up to 120°C, highlighting ongoing challenges in developing stable semiconductor lasers.
In sum, the photonic silicon chip is novel because it’s the first demonstration of a fully monolithic laser diode on a silicon wafer of this size. The team’s process is also scalable and cost-effective.
Tejasri Gururaj is a freelance science writer and journalist with a master’s degree in physics.
Published – April 15, 2025 05:30 am IST